Abstract
Plasma nitriding improves the wear resistance of a material by effectively altering the surface microstructure while maintaining adequate substrate properties.
Nitriding occurs when a bias voltage is applied to the work piece causing ions to collide with the surface and consequently creating the nitride effect.
Nitriding is a thermochemical surface treatment used in steels and alloys to improve wear and friction properties by surface microstructure modification, while maintaining adequate substrate properties. Not only wear resistance is improved, but also corrosion and fatigue resistance may be increased by the same treatment. Plasma nitriding is the most versatile nitriding process and has many advantages over conventional salt-bath and gas nitriding. The close control of the metallurgical properties of the nitrided surface is the most important advantage of the plasma nitriding process. Nowadays duplex and hybrid layers are growing in importance, requiring prior plasma nitriding of the substrate to avoid compound layer formation.
Plasma nitriding or ion nitriding is a modern process used to impart surface hardening to metals for a wide variety of applications. As the name implies, the process is carried out in a plasma media containing ionized nitrogen alone, or in combination with other gasses to react with the work surface. The process was independently patented by Egan (1931), and Berghaus (1932, 1939), and advances in the field of power electronics have caused the process to gain World-wide popularity in a variety of applications.
One outstanding advantage of plasma heat treatment is the lower environmental impact it poses compared with heat treatment with a controlled atmosphere furnace. For example, nitriding with a controlled atmosphere furnace often uses ammonia gas. In contrast, using a plasma nitriding technique, a steel material can be nitrided with nitrogen and hydrogen. Also, with plasma nitriding, the intended work-piece alone is heated without heating the entire interior of the furnace—a practice necessary for a controlled atmosphere furnace.
Figure 1 shows schematics of typical plasma heat treatment equipment configurations. With cold-wall or hot-wall configurations where a bias voltage is applied to a work-piece, a clean surface is exposed on the work-piece through sputtering where ions collide with the work-piece. Consequently, the surface of a material is nitrided in a short time even if the material type needs a longer time for nitriding with a gas nitriding or vacuum nitriding process.
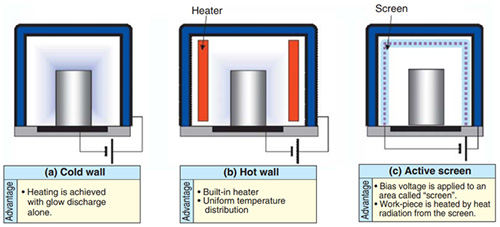
Figure 1: Schematic diagram of plasma heat treating equipment
The advantages of plasma nitriding can be summarized as follows:
1. Plasma nitriding is essentially faster than other conventional nitriding techniques.
2. Proper control of the temperature, atmosphere composition, and discharge parameters can lead to production of superior microstructure and permit better control over the composition of the final product surface, its structure, and its properties.
3. Plasma nitriding is environmentally non polluting.
4. Unlike conventional nitriding treatments the process can operate at a temperature as low as 350°C. Low temperature nitriding allows high surface hardness to be achieved along with the maintenance of high core strength in low temperature tempering steels. Furthermore, treating at these low temperatures keeps distortion to a minimum.
There are a few disadvantages of the plasma nitriding process:
- Cleanlinnes of surface of the components is essential to hinder unstable arc discharges forming during the heating cycle.
- The need to fixture parts to avoid overheating.
- Because of power/surface area relationships. Components with similar size may not be plasma nitrited in one batch.
- The high initial plasma cost.