Abstract
From the numerous heat treatment procedures for hot-work steels, two examples of proprietary steels have been selected, together with some basic guidelines for their application and comparison with standard grades.
Bofors RO 8155 owes its existence primarily to its serving as a substitute for the more expensive ASTM grade H 13 which it has successfully replaced in a number of instances. Bofors QRO 45 is relatively low alloy steel: the low-alloy content being the result of stringently optimizing the composition with reference to the overall properties of the steel.
From the numerous heat treatment procedures for hot-work steels, two examples of proprietary steels have been selected, together with some basic guidelines for their application and comparison with standard grades.
Bofors RO 8155
This steel has no direct equivalent among the standardized steels. It owes its existence primarily to its serving as a substitute for the more expensive ASTM grade H 13 which it has successfully replaced in a number of instances.
The steel is normally supplied heat treated to a hardness of 330-360 HB. As may be seen from the curves in Figure 1 it has excellent hardenability, i.e. on oil quenching, the steel is practically through-hardening in dimensions up to 200 mm in diameter.
The mechanical properties of the steel, both as oil quenched and tempered and as air hardened and tempered, respectively, are shown in Figure 2. As may be seen from the curves in Figure 3 the steel has high strength at elevated temperatures, i.e. up to about 500°C.

Figure 1. Curves showing depth of Bofors RO 8155. Specimens 200 mm diameter,
oil quenched from 900°C. Tempered at 400, 500 and 600°C for 1 h
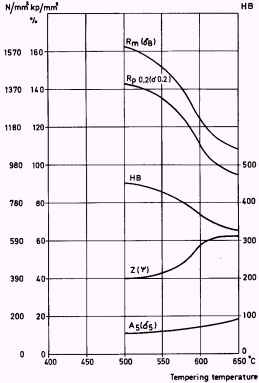
Figure 2. Curves showing various mechanical properties of Bofors RO 8155, oil quenched from 900°C and tempered. Specimen 200 mm diameter. Location of test-piece: 1/2 radius
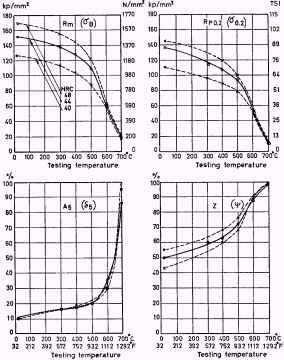
Figure 3. Mechanical properties at elevated temperatures of Bofors RO 8155.
Air hardened from 900°C and tempered to various hardnesses One of the uses of the steel is for drop-forging dies (see Figure 4). In this capacity it often has a longer service life than grade H 13. This is probably due to the superior thermal conductivity of RO 8155. Another use to which the steel is put is as material for supporting dies in the extrusion of aluminium. The hardness should be 44-47 HRC. The steel is well suited to nitriding.
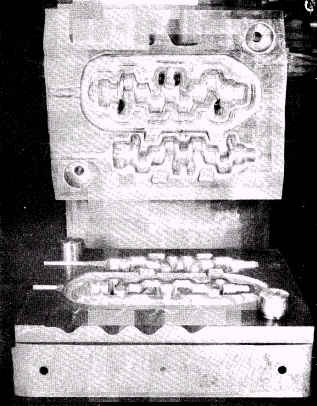
Figure 4. Drop-forging dies or motor-car crankshafts. Dies made from Bofors RO 8155 Bofors QRO 45
The composition of the steel corresponds to BS BH 10A. It is relatively low alloy steel: the low-alloy content being the result of stringently optimizing the composition with reference to the overall properties of the steel.
It possesses good hot-wearing properties, low susceptibility to fatigue cracking and high elevated-temperature strength. In the great majority of instances QRO 45 serves as a wholly satisfactory substitute for the previously very popular 5% and 9% tungsten steels, respectively.
The hardening temperature is the same as for grade H 13, that is temperature of 1000-1050°C, and 20-30 min is a satisfactory holding time at the hardening temperature. Longer times or temperatures higher than 1050°C tend to make the steel coarse-grained (see Figure 5). Compared with grade H 13, QRO 45 has a greatly superior resistance to tempering, which can be seen in Figure 6. At temperatures around 600°C and above, the elevated-temperature strength of Q R 0 45 is higher than that of grade H 13 (see Figure 7).
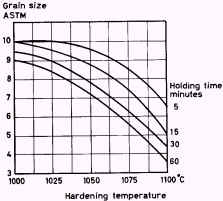
Figure 5. Influence of hardening temperature and holding time on grain size of BH 10A Typical fields of application for QRO 45 are dies for die casting and hot forging of brass, mandrels and dies for the extrusion of copper, tools for the hot-upsetting of steel bolts and nuts. For this last example the wear resistance of the steel can be greatly improved by nitriding or by case hardening. Owing to the low hardness of QRO 45 as annealed, cold hobbing is a feasible alternative process for shaping tools of suitable design (see Figure 8).
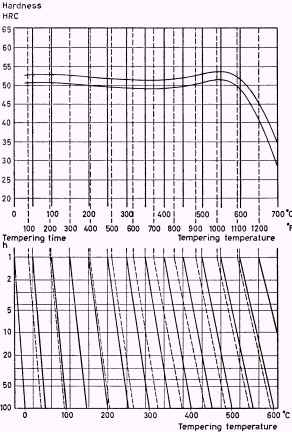
Figure 6. Tempering curves showing interdependence of time and temperature for Bofors QRO 45.
Oil or air hardened from 1050°C
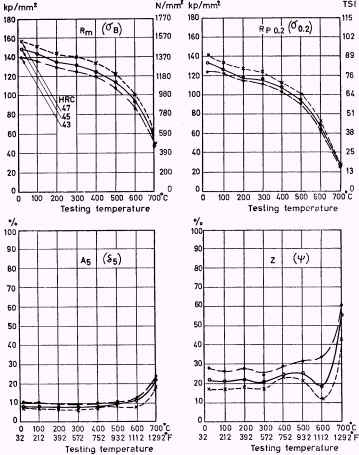
Figure 7. Mechanical properties at elevated temperatures of BH 10A, air hardened from 1050°C and
tempered to various hardnesses
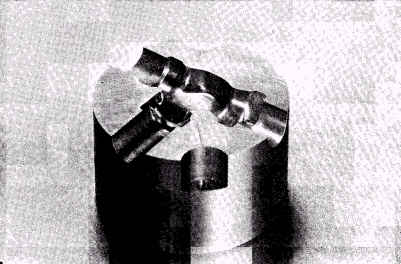
Figure 8. Cold hobbed die made from BH 10A. Used for brass die-casting.