Abstract
Titanium alloys have an extremely wide appeal due to a range of advantages including a very high strength to weight ratio, high fatigue resistance and biocompatibility.
One specific method of gas nitriding still being developed today is laser gas nitriding (LGN) whereby the erosion wear resistance can be significantly increased in titanium alloys.
The nitrided layer is formed on the surface of the titanium alloy as a result of the diffusion process. The surface differs from that achieved through oxidising in that a useful, hard compound layer structure is created. The nitrided alloy consists of several layers, including compound layer, diffusion zone and core material. The phases of the transition on the surface of the nitrided titanium alloy can be written as: Ti→ Ti(N) → Ti2N → TiN where Ti(N) denotes titanium with nitrogen in solid solution. The grain growth and thickness of the nitrided layer depend on two main parameters: nitriding temperature and time.
Among the many methods of surface modification of titanium alloys, one of the most efficient is laser gas nitriding (LGN).
Although the LGN method was invented in 1983, it is still being developed. The reason for this is the continuous development of laser devices and associated with this advances in laser technology. The LGN process for titanium and titanium alloys has been widely studied by scientists, and also there are plenty of articles in this field. However, most of the articles concern the structure, morphology, corrosion resistance, tribology and mechanical properties of the surfaced layers produced by gaseous CO2 and solid-state YAG lasers. There are only a few publications on the application of high-power diode lasers (HPDLs) in the process of titanium nitriding and also there is no information on the erosion wear resistance of surface layers nitrided by HPDLs.
Y. Fu et al. have studied different methods for improving the erosion resistance of pure titanium. They have found that the laser surface treatment of titanium in a nitrogen atmosphere provides the best results and a significant improvement of the erosion resistance compared to other methods of surface treatment and the deposition of surface lasyers.
In the work of A.Lisiecki and A.Kurz-Lisiecka, a novel continuous wave (CW) HPDL emitted in the near-infra-red band at 808 nm, with a rectangular laser beam spot and a uniform energy distribution across the spot was applied for producing surface layers on the titanium alloy Ti6Al4V during LGN. The erosion wear resistance of the Ti6Al4V alloy before and after the LGN process at different angles of incidence was investigated. It was found that the erosion wear resistance of the composite surface layers is significantly higher than the substrate of titanium alloy Ti6Al4V. The erosion wear resistance depends on the angle of incidence. Reducing the angle of incidence decreases the weight loss of the composite surface layers and simultaneously increases the weight loss of the Ti6Al4V. It was found that the weight loss of the composite surface layer with the highest resistance is over six times lower compared to the Ti6Al4V, at an incident angle of 15°.
Introduction of the new generation of high power direct diode lasers (HPDDL) to industry allows for further development of the laser surface modification of titanium alloys.
The most commonly used titanium alloy Ti6Al4V (wt.%, Grade 5) was chosen for surface modification during laser gas nitriding, Table 1 and 2. Additionally the commercially pure titanium (Grade 2) was chosen as a reference sample (comparative). Laser gas nitriding tests were performed by means of a prototype experimental stand consisted of four-axis computer numerical controlled (CNC) system and a novel high power direct diode laser (HPDDL) ROFIN DL020 with a rectangular beam spot.
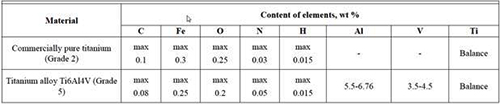
Table 1: Chemical composition of the commercially pure titanium (Grade 2) and the titanium alloy Ti6Al4V (Grade 5) according to the standard ASTM B 265-99
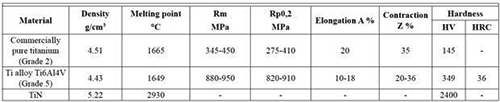
Table 2: Physical and mechanical properties of commercially pure titanium, titanium alloy Ti6Al4V and titanium nitride TiN
The specimens of titanium alloy Ti6Al4V were cut from a hot-rolled rod with a diameter of 50.0 mm. Next the disks were machined by milling and turning to a nominal diameter of 46.0 mm and a thickness of 3.0 mm. In turn, the specimens of commercially pure titanium were cut from a flat sheet 3.0 mm thick and then the specimens were machined to a predetermined dimension of test disks. Prior to the laser nitriding the test disks were mechanically ground and rinsed with acetone. Disks were mounted in a rotary drive and set horizontally. The rectangular laser beam was focused on the top surface of disk specimens and set transversely to the travel direction. Pure gaseous nitrogen was fed through a cylindrical nozzle with a diameter of 12 mm. The nitrogen flow rate was kept at 18 l/min.
The nitrided single beads had a diameter of 30 mm. The test nitrided surface layers were produced at constant scanning sped of 200 mm/min and different laser output power from 400 to 1000 W, thus different heat input. Additionally, the time of laser beam interaction on the treated surface of titanium alloy was calculated for the beam spot width of 1.8 mm and scanning speed 200 mm/min. Previous investigations of the HPDDL nitriding of titanium alloys revealed that the time of integration is an important factor that influences significantly on the process of nitriding even at constant heat input.
This study has shown that the laser gas nitriding of titanium alloy Ti6Al4V by the HPDDL laser leads to a significant increase in wear and friction characteristic. Surface layers produced during HPDDL nitriding are cracks free. The tribological characteristics of the nitrided surface layers are related to the processing parameters and thus to the surface topography, morphology and phase composition. Surprisingly the wear resistance of nitrided surface layers during ballon-disk test is not directly correlated to microhardness. The highest wear resistance showed the test surface layer produced at the minimum laser power (thus minimum heat input) and characterized by the lowest Vickers microhardness. The mechanism of wear is combined adhesion and abrasion.