Abstract
Any strain aging process is heavily dependent on both time and temperature, with temperature for example having a strong influence on solute diffusion and binding energy along with the movement of dislocations.
This article takes a closer look at tensile testing of materials at high temperatures and uses the appearance of serrations as a key measure of dynamic strain aging.
Dynamic strain aging (DSA) is a phenomenon in metals and alloys resulted from the interaction between the diffusing solute atoms and the moving dislocation. It has been found that DSA occurs in many alloys during uniaxial tension or compression process. In traditional metal forming process, such as extrusion and rolling, it is difficult to control the DSA process because of the limited deformation time and deformation reduction.
In the paper of O.H.Ibrahim and I.S.Ibrahim the effects of test temperature and strain rate on DSA behavior of Hastelloy X was studied. Tensile testing was first performed over a temperature range of 22-700 °C and strain rate of 10-3 s-1. The alloy exhibited features of dynamic strain aging represented by welldefined serrations in the stress-strain curves at 550 and 650 °C. No serrations were noticed at temperatures below 550 °C and above 650 °C at a strain rate of 10-3s-1. The frequency of serrations increased with progressive deformation up to the point of failure at each temperature. In order to test out the strain rate effect, additional tensile tests were performed at a slower strain rate of 10-5 s-1 at 550 and 650 °C. The increase in test temperature from 550 to 650 °C and the decrease in strain rate from 10-3 to 10-5s-1 decreased the amount of both the flow stress and strain of the material. The intensity, frequency, and amplitude of the serrations increased with the decrease in strain rate and increase in temperature. The type of serrations was associated with the applied temperature and strain rate. Fracture surface examination indicated a change from ductile dimpled rupture at room temperature into ductile-brittle mixed mode at 650 °C.
Figure 1 shows stress–strain curves of Hastelloy X after tensile testing over a temperature range of 22-700 °C and strain rate of 10−3 s−1. Stress–strain curves displayed smooth appearance at room temperature and up to 450 °C and at 700 °C. Serrated tensile flow was observed in the stress–strain curves at temperatures of 550 and 650 °C indicating the onset of dynamic strain aging which is referred to as the Portevin-Le Chatelier (PLC) effect. The frequency of serrations increased with the progress in deformation both at 550 and 650 °C. The amplitude of serrations in the stress strain curve increased with the increase in temperature from 550 to 650 °C. In general, a decrease in the mount of flow stress and strain can be observed with the increase in test temperature from 22 to 700 °C. The value of the yield stress dropped 40% from 322 to 192 MPa whereas the ultimate tensile strength value only dropped 35 % from 710 to 460 MPa. The total elongation decreased from 63 % to 43% i.e. by about 30%.
The effect of temperature and strain rate on the dynamic strain aging behaviour of Hastelloy X is shown in Figures 2 and 3. In Figure 2, testing at a strain rate of 10-3 s-1 shows that the rise in temperature from 550 to 650 °C resulted in a reduction in the flow stress and strain. The yield and ultimate stress values dropped 20 and 10 %, respectively whereas the strain decreased by 18 %. The strain hardening exponent (n) decreased as well from 0.51 to 0.48. Figure 3 shows results of testing at strain rate of 10-5s-1. The increase in test temperature from 550 to 650 °C decreased the yield stress and the ultimate tensile strength values by 30 and 15%, respectively. The elongation decreased by 15%. The corresponding strain hardening exponents were 0.42 and 0.38, respectively.
The results of the tensile properties at a strain rate of 10-3 and 10-5 3s-1 of Figures 2 and 3 are summarized in Table 2. As can be shown in Figures 2 and 3 the frequency and the amplitude of serrations in the stress–strain curves increased with the increase in temperature and decrease in strain rate.
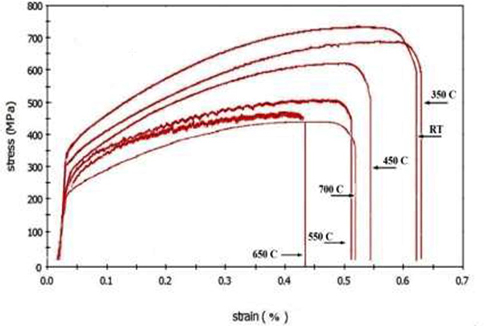
Figure 1: Stress- Strain Curves at A Strain Rate of 10-3 s-1 at Various Test Temperatures
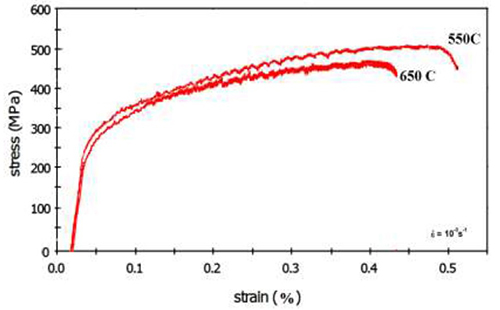
Figure 2: Stress-Strain Curves of Hastelloy X Tested at 550 And 650°C at A Strain Rate of 10-3s-1
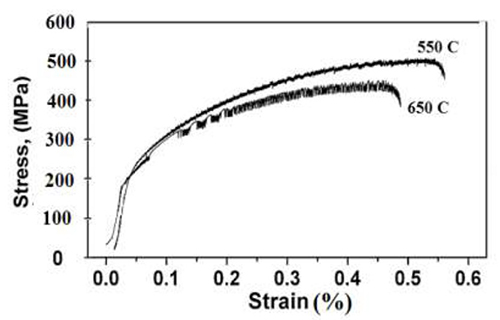
Figure 3: Stress-Strain Curves of Hastelloy X Tested at 550 And 650 °C at A Strain Rate of 10-5s-1
As can be seen in Figure 2 the type of serrations changed from type A at 550 to type B at 650 °C whereas in Figure 3 the serrations changed from type B at 550 to type C at 650 °C.
The aim of the study of N.Lin, K.Yang, S.Zeng and W.Chen was to analyze the micro-mechanism on DSA of the AZ91D pressed magnesium alloy to display its rule of plastic instabilities. Cylindrical tensile specimens were machined from round rod. The specimens had a gauge length of 30 mm and a diameter of 6 mm. Before subjecting specimens to any deformation, the rods were treated by solid solution at 683 ± 3 K for 24 h to ensure the aluminum atoms completely diffused into the α-Mg matrix. Tensile tests were carried out on an Instron1185 machine in the temperature range from 248 K to 423 K within the strain rate range from 1.11×10-4 s -1 to1.67×10-3 s -1. The micro-structure observations were performed using a XL30 -ESEM scanning electron microscopy (SEM).
The DSA occurs when the AZ91D magnesium alloy is treated under different temperature for as-solid-solution treated at the strain rate of 1.11×10-4 s -1 (see the recorded stress-strain curve Figure 4). It can be seen that the stress-strain curve was not smooth but occurred serrated yield, when the strain be to a certain value which called the critical strain as εc, and the εc was decreasing with the temperature increasing at a constant strain rate. Test results show the treated AZ91D Mg alloy occurred serrated yield at a set stain rate range from 1.11×10-4 s -1 to1.67×10-3 s -1, the εc was increasing with the strain rate increasing. Moreover, the temperature range of DSA was drifting to high temperature (as showed in Table 1).
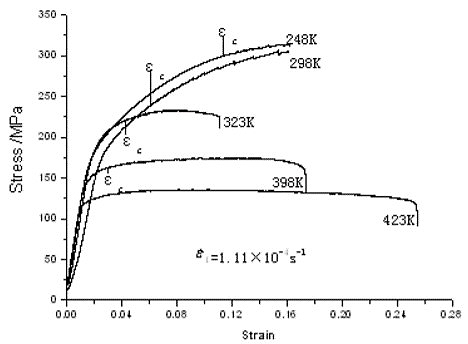
Figure 4: Stress-strain curve under different temperature for as-solid-solution treated AZ91D Mg alloy at the strain rate of 1.11×10-4 s-1

Table 1: The occurrence of serrated flow phenomenon