Abstract
The Direct Nickel (DNi) Process revolutionizes nickel extraction by utilizing nitric acid as a leaching agent to process all types of nickel ore through a single flow sheet, producing multiple saleable products. This atmospheric hydrometallurgical process demonstrates exceptional environmental efficiency by recycling over 95% of the nitric acid used. Unlike conventional extraction methods that require different approaches for different ore types, the DNi Process offers a versatile solution for the nickel mining industry, combining economic viability with environmental responsibility through its innovative acid recovery system and multiple valuable by-products.
Introduction to Nickel Ore Processing
Nickel ore deposits exist in two primary forms: nickel sulphides and oxidic nickel laterites. Traditional nickel extraction employs three distinct processes depending on the ore type. For laterite ores, conventional pre-concentration techniques are ineffective because nickel distributes throughout iron oxides and clays, unlike sulphide ores where nickel appears in discrete minerals. Currently, limonitic ores undergo acid leaching (hydrometallurgical process), saprolite ores require smelting (pyrometallurgical process), and limonite-saprolite blends are processed using the Caron process (a combined pyro/hydrometallurgical approach).
The Direct Nickel Process: Overview and Advantages
The Direct Nickel Process (DNi) represents a significant advancement in nickel processing technology. As an atmospheric hydrometallurgical process, it can treat all nickel laterite ore types using a single flow sheet to produce multiple saleable products. The key innovation lies in using nitric acid as the leaching agent coupled with a patented recovery system that recycles more than 95% of the acid, creating both economic and environmental benefits.
The DNi Process begins with mining and comminution, where ore is crushed to less than 2mm particle size. This prepared ore is then mixed with nitric acid to create a slurry containing 20-30% solids. The mixture enters leaching tanks heated to 110°C with a typical residence time of 4 hours (range: 2-6 hours).
During leaching, approximately half of the ore mass dissolves into the nitric acid, leaving behind acid-insoluble minerals (primarily silicates) and creating a pregnant leach solution (PLS). The post-leached slurry undergoes solid-liquid separation through a series of counter-current decantation thickeners. The separated acid-insoluble residue is washed and filtered before being transferred to a storage facility.
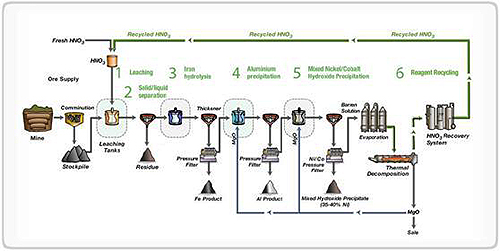
Figure 1: The Direct Nickel Process - Simplified Schematic
Metal Recovery and By-Product Generation
Following the separation stage, the PLS enters the iron hydrolysis circuit where it's heated in atmospheric tanks. This process distills off nitric acid for recovery while simultaneously forming hematite (Fe₂O₃) in the tanks, effectively removing iron and chromium from the solution. The resulting slurry is filtered to produce a washed hematite filter cake—a valuable by-product.
The iron-free solution then receives magnesia (MgO) slurry treatment to increase pH and precipitate aluminum hydroxide, which is filtered to produce an aluminum product. The low-aluminum solution proceeds to mixed hydroxide precipitation, where magnesia slurry is again used in a two-stage circuit to precipitate the mixed hydroxide product (MHP) containing most of the recovered nickel and cobalt.
This MHP slurry undergoes thickening to separate the solid product from the barren solution. The MHP is then filtered and washed to produce the primary saleable product. Additional processing modules using proven technologies can convert this intermediate product into nickel and cobalt metal, oxides, or sulfides, depending on market requirements.
Acid Recovery and Environmental Sustainability
In the final stage, the barren solution—primarily containing magnesium nitrate and water—undergoes evaporation to recover clean water for reuse. The concentrated magnesium nitrate (containing 2-3 moles of water) feeds into a thermal decomposition unit where it breaks down into magnesium oxide and nitrogen oxide gases.
A portion of the produced MgO recycles back into the process, with the remainder available as a saleable product. The nitrogen oxide gases pass through a series of absorption stages that convert them to nitric acid, which returns to the leach circuit, completing the remarkably efficient recycling loop that defines the DNi Process.