Abstract
The copper flash smelting process represents a significant advancement in pyrometallurgical processing of metal sulphide concentrates, particularly for copper and nickel. Developed by Outokumpu Oy in 1948, this technology enables controlled oxidation of iron and sulfur while generating substantial heat for efficient melting of solids. The process involves injecting fine copper sulphide concentrate with oxygen-enriched air into a specialized furnace at approximately 1500K, resulting in copper-rich matte production. This process has become increasingly important in modern metallurgical operations due to its efficiency and environmental advantages.
Process Overview and Historical Development
Flash smelting is a pyrometallurgical process primarily used for smelting copper sulphide concentrates, though it has significant applications in nickel sulphide concentrate processing. The technology, developed by Finnish mining company Outokumpu Oy from 1948 onwards, saw widespread adoption by mid-1971 as numerous mining companies acquired licenses and established processing plants.
Advantages Over Traditional Methods
Unlike reverberatory furnace smelting, where sulphide oxidation primarily occurs in converters and matte grade depends on concentrate analysis, flash smelting enables predetermined sulphide oxidation degrees. The process utilizes oxidation reaction heat to maintain furnace heat balance, potentially achieving autogenous operation when iron and sulphur contents are sufficiently high.
Process Fundamentals
Copper flash smelting involves injecting fine, dried copper sulphide concentrate and silica flux with air, oxygen-enriched air, or oxygen blast into a hot furnace (≈1500K). This process triggers rapid reactions between sulphide minerals and oxygen, resulting in:
- Controlled oxidation of Fe and S from the concentrate
- Substantial heat generation
- Efficient solids melting
Process Outputs
The process yields three primary products:
- Molten copper-rich Cu-Fe-S matte (45-65% Cu), containing most copper from the concentrate plus unoxidized Fe and S
- Molten slag containing iron oxide, gangue, and flux oxides
- Off-gas comprising SO2, N2, and potentially CO2 and H2O if supplementary fossil fuel is used
Raw Materials
The main inputs include:
- Copper concentrate
- Silica flux
- Air
- Industrial oxygen
Chemical Reactions and Thermodynamics
The fundamental reactions occurring in the flash furnace can be represented by the following equations:
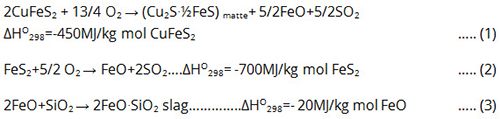
These reactions are characterized by their strongly exothermic nature, providing the majority or entirety of energy required for:
- Heating the furnace contents
- Melting the charge materials
- Superheating the furnace products
When industrial oxygen or highly oxygen-enriched air is employed as the oxidant source for these reactions, the process can operate with minimal or no additional fossil fuel combustion in the furnace. This characteristic makes the process particularly energy-efficient compared to traditional smelting methods.
The heat generated from these oxidation reactions is crucial for maintaining the furnace heat balance. In cases where the concentrate contains sufficiently high levels of iron and sulphur, the smelting process can become autogenous, meaning it can sustain itself thermally without external fuel input.
Concentrate Characteristics
The feed materials typically undergo flotation concentration before reaching the smelter. The optimal particle size range of 50-100 μm is ideal for flash smelting, requiring only drying before furnace entry. Common minerals include:
- Chalcopyrite (CuFeS2)
- Pyrite (FeS2)
- Bornite (Cu5FeS4)
- Chalcocite (Cu2S)
- Covellite (CuS)
- Quartz (SiO2)
Typical concentrate compositions contain 20-30 mass % Cu, 25-35% Fe, and 25-35% S.
Furnace Operation
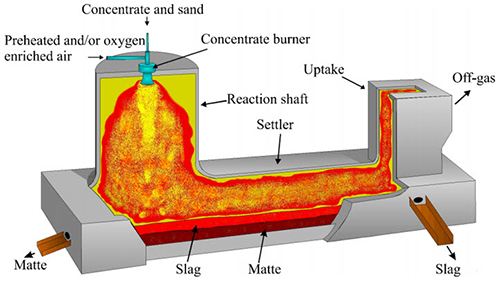
Figure 1: Flash smelting furnace
The flash smelting furnace features hydrocarbon fuel burners positioned concentrically in the reaction shaft. These burners maintain optimal temperature conditions for proper reaction rates and concentrate melting. Process efficiency largely depends on dry concentrate composition, particularly the mixture of Cu2S and CuFeS2.