Abstract
This article examines the brazing techniques for titanium and its alloys, focusing on their application in joining dissimilar materials. While titanium's high strength-to-weight ratio and corrosion resistance make it valuable for various industrial applications, joining challenges have historically limited its use. The discussion covers various brazing filler metals, process considerations, and technological developments since the 1950s, particularly emphasizing vacuum brazing techniques and the importance of controlling thermal cycles to maintain material properties.
Introduction to Brazing Technology
Titanium and its alloys excel in corrosion resistance and strength-to-weight performance, making them ideal for corrosion-resistant applications and strength-efficient structures. Commercially pure titanium (CP-Ti) serves extensively in fabricating tanks, heat exchangers, reactor vessels, and power generation equipment.
Historical Development and Applications
Titanium brazing development began in the 1950s, primarily driven by aerospace requirements for lightweight structures. The industry has since developed over 100 brazing filler metals (BFM) to address various joining challenges, particularly focusing on titanium-to-titanium and titanium-to-stainless steel connections.
Brazing Filler Metal Classifications
All known titanium brazing filler metals can be roughly separated into five major families according to the base component in their chemical compositions, as shown in Table 1 below.
Table 1: Major families of brazing filler metals for joining titanium alloys
Brazing filler metals |
Brazing temperature ranges, [°C] |
Silver based |
720–950 |
Titanium based |
850–1020 |
Aluminum based |
600–750 |
Palladium based |
1050–1150 |
Zirconium based |
790–950 |
The nature of titanium alloys (base metals) determines important temperature/time limits of brazing thermal cycles. These limits are caused by undesirable changes in the microstructure and properties of both the base metal and the joint:
- Due to beta-transus, i.e., the critical temperature of the α ↔ β phase transformation, and
- Due to the formation of brittle intermetallics at the interface between the base metal and brazed joint.
Process Limitations and Considerations
The nature of titanium alloys imposes critical temperature and time limits during brazing cycles. These constraints arise from two primary factors: the beta-transus temperature (marking the α ↔ β phase transformation) and the potential formation of brittle intermetallics at the interface between base metal and brazed joint. This consideration becomes particularly crucial for thin-wall structures common in aerospace applications.
Brazing Techniques and Environment
Vacuum brazing has emerged as the predominant method for titanium joining, primarily due to the metal's requirement for protection against oxidation. Alternative approaches include silver chloride-lithium fluoride fluxes and TIG brazing for specific applications.
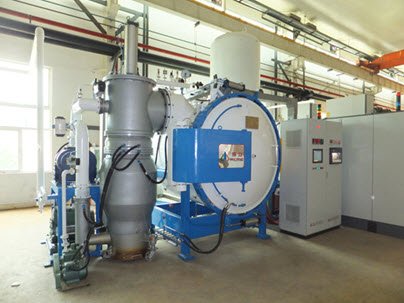
Figure 1: Horizontal high vacuum brazing furnace
Silver-based brazing alloys were the first successfully applied to titanium. These include commercially pure silver and various silver alloys containing copper, manganese, zinc, and tin. While these joints exhibit good ductility, they show limited strength at elevated temperatures and poor corrosion resistance in chloride-containing environments.
Silver alloy braze metals offer an important advantage: their liquidus temperature falls below the beta transus of alloys such as Ti-6Al-4V, minimizing effects on base metal microstructure and properties. Similarly, aluminum-silicon fillers enable low-temperature brazing while reducing overall weight. However, maintaining brief brazing cycles remains crucial to prevent brittle intermetallic formation.
Process Optimization and Control
Successful titanium brazing requires precise control of process parameters, particularly temperature and time cycles, to maintain material properties while achieving strong, reliable joints. The selection of appropriate filler metals and brazing conditions depends heavily on specific application requirements and service conditions.