Abstract
High-pressure acid leaching (HPAL) represents a critical hydrometallurgical process for recovering nickel from laterite ores. As global nickel sulfide deposits decrease, HPAL's importance grows, particularly given that lateritic ores constitute the majority of worldwide nickel and cobalt resources. This article examines the HPAL process, including its operating parameters, chemical reactions, and applications in metal recovery. The process demonstrates particular effectiveness in treating limonitic ores with high iron content and low magnesium and silica concentrations, offering significant advantages through acid regeneration during processing.
Introduction to HPAL Technology
The increasing strain on natural resources has elevated the importance of high-pressure acid leaching in metal recovery operations. While primarily utilized for nickel extraction from laterite ores, the process also effectively recovers copper and cobalt. As sulfide-based nickel production decreases, HPAL's role in processing lateritic ores, which contain most of the world's nickel and cobalt resources, becomes increasingly critical.
Process Fundamentals and Applications
Traditionally, laterite ores underwent pyrometallurgical treatment. However, hydrometallurgical processing through direct acid leaching at temperatures exceeding 240°C has emerged as a viable alternative for modern mining projects. The process particularly suits limonitic ores with high iron content and low magnesium and silica concentrations.

Figure 1: Basic steps in the HPAL process
Operational Parameters and Processing Steps
The HPAL process begins with ore crushing and screening, where operators evaluate potential beneficiation through silica fraction separation. The beneficiated product enters titanium-lined autoclaves for sulfuric acid leaching at temperatures between 240-270°C, generating equilibrium vapor pressures of 33-35 atm. Key operational parameters include:
- Pulp density: 25-35% solids
- Residence time: 30-90 minutes
- Temperature range: 246-270°C
- Acid consumption: 200-520 kg/t per dry ore
- Pressure: 3800-5400 kPa
Chemical Reactions and Metal Recovery
FeOOH(s) + 3H+(aq) = Fe3+(aq) + 2H2O(aq) (1)
AlOOH(s) + 3H+(aq) = Al3+(aq) + 2H2O(aq) (2)
NiO(s) + 2H+(aq) = Ni2+(aq) + H2O(aq) (3)
CoO(s) + 2H+(aq) = Co2+(aq) + H2O(aq) (4)
2Fe3+(aq) + 3H2O(aq) = Fe2O3(s) + 6H+(aq) (5)
Fe3+(aq) + SO42- + H2O(aq) = FeOHSO4(s) + H+(aq) (6)
2FeOHSO4(s) + H2O(aq) = Fe2O3(s) + 2SO42- + 4H+(aq) (7)
3Al3+(aq) + 2SO42- + 7H2O(aq) = (H3O)Al3(SO4)2(OH)6(s) + 5H+(aq) (8)
Al3+(aq) + SO42- + H2O(aq) = AlOHSO4(s) + H+(aq) (9)
Iron (in the trivalent state) and aluminum follow a dissolution-precipitation path, forming solid products. Iron in the form of goethite (α FeOOH) and aluminum in the form of boehmite (AlOOH) dissolve initially to soluble ferric and aluminum sulfates respectively, according to equations (1) and (2). Gibbsite (Al(OH)3), the major aluminium phase in the limonite ore, is transformed to boehmite at around 135-155°C. Nickel and cobalt in the assumed form of oxides, dissolve according to the reactions (3) and (4) respectively and remain in the aqueous phase as sulfates.
Ferric cations hydrolyze after the dissolution of goethite, forming hematite or basic ferric sulfate, as indicated by the reaction (5) and (6). Basic ferric sulfates transform to hematite (7). Basic ferric sulfates formation depends on leaching conditions and it is favored by highly acidic environment. Higher temperature, on the other hand, favors the formation of hematite.
These reactions regenerate the acid consumed by goethite dissolution, which is one of the important advantages of the HPAL process. Aluminum cations also hydrolyze, leading to the formation of solid products. Again, most of the acid consumed by boehmite dissolution is regenerated, as shown in equations (8) and (9). The autoclave product is a hot slurry, typically at 20-25% solids, containing typically 4-6 g/l nickel, 30-60 g/l sulfuric acid, <8 g/l iron and <3 g/l aluminum.
Final Processing and Output
The autoclave discharge produces a hot slurry (20-25% solids) containing approximately 4-6 g/l nickel, 30-60 g/l sulfuric acid, <8 g/l iron, and <3 g/l aluminum. This undergoes solid/liquid separation through counter-current decantation, typically utilizing six to seven thickener stages. Most HPAL facilities generate their sulfuric acid by burning elemental sulfur, utilizing the byproduct steam in various operations.
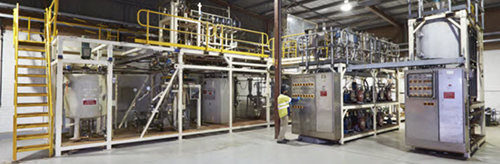
Figure 2: High Pressure Acid Leach equipment