Abstract
Austempered Ductile Iron (ADI) represents a significant advancement in materials engineering, combining superior mechanical properties with cost-effective manufacturing. This heat-treated form of ductile iron is gaining prominence in automotive and industrial applications due to its exceptional strength, toughness, and economic advantages compared to traditional steels and aluminum alloys. Through the precisely controlled austempering process, ADI achieves a unique microstructure that delivers enhanced mechanical properties, including improved tensile strength, fatigue resistance, and wear characteristics. This article examines the manufacturing process, properties, and diverse applications of ADI, highlighting its growing importance in modern engineering solutions.
Understanding Austempered Ductile Iron: Properties and Composition
Austempered Ductile Iron (ADI) represents a revolutionary development in cast iron technology, offering mechanical properties that surpass conventional cast irons while maintaining economic competitiveness with steels and aluminum alloys. This engineered material begins as ductile iron, containing more than 2% carbon present in spheroidal graphite form, which undergoes a specialized heat treatment process called austempering. Unlike gray iron, where graphite appears as individual flakes, ADI's spheroidal graphite structure contributes to its superior mechanical properties, including linear stress-strain behavior and enhanced ductility.
The Austempering Process: A Technical Overview
The transformation of ductile iron into ADI occurs through a precisely controlled heat treatment process. This process involves austenitizing, quenching, and austempering stages, each critical to developing the desired microstructure of acicular ferrite and carbon-stabilized austenite. Small amounts of alloying elements such as nickel, molybdenum, or copper are added to improve hardenability. The resulting ausferrite structure can undergo strain-induced transformation to martensite under local stress, creating wear-resistant regions within the material.
Manufacturing Excellence: The ACP Austempering Method
Advanced Cast Products (ACP) employs specialized salt bath techniques for superior dimensional control throughout the austempering process. The procedure follows these critical stages:
- Austenitizing (1550-1700°F): Castings are heated in a molten salt bath to form fine-grain austenite with uniform carbon distribution.
- Controlled Quenching: Rapid cooling prevents pearlite formation while maintaining temperatures above martensite formation point.
- Austempering: Final salt bath treatment at precisely controlled temperatures and times develops the desired ausferrite structure.
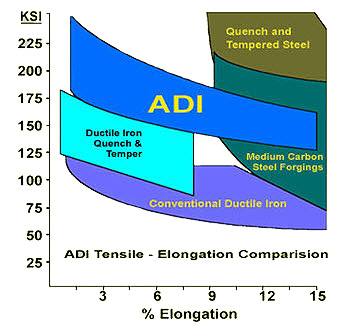
Figure 1: Steps in the ACP Austenitizing Process
Superior Performance Characteristics
ADI offers distinct advantages over traditional materials:
- Comparable strength and toughness to heat-treated steels
- Enhanced vibration dampening and heat transfer properties
- 9% lighter than steel with minimal draft requirements
- Superior low-temperature performance
- Excellent work-hardening capabilities
- Cost-effective manufacturing compared to steel and aluminum alternatives
Industrial Applications and Market Impact
ADI's versatility has led to its adoption across numerous industries:
- Agricultural equipment requiring soil wear resistance
- Heavy machinery components including digger teeth
- Industrial pumps and wear-resistant components
- High-performance gearing systems
- Construction equipment
- Food processing machinery
Table 1. British Standards Specification for ADI EN 1564: 1997
Material Symbol |
Number |
Tensile Strength N/mm² (min) |
0.2% Proof Stress N/mm² (min) |
Elongation % (min) |
EN-GJS-800-8 |
EN-JS1100 |
800 |
500 |
8 |
EN-GJS-1000-5 |
EN-JS1110 |
1000 |
700 |
5 |
EN-GJS-1200-2 |
EN-JS1120 |
1200 |
850 |
2 |
EN-GJS-1400-1 |
EN-JS1130 |
1400 |
1100 |
1 |
Table 2. Standard ADI Grades (USA) ASTM 897-90
Grade |
Tensile Strength (min) |
Yield Strength (min) |
Elongation % |
Impact Energy * |
Typical Hardness BHN |
1 |
125 Ksi / 850 N/mm² |
80 Ksi / 550 N/mm² |
10% |
75 Ft-lbs / 100 Joules |
269-321 |
2 |
150 Ksi / 1050 N/mm² |
100 Ksi / 700 N/mm² |
7% |
60 Ft-lbs / 80 Joules |
302-363 |
3 |
175 Ksi / 1200 N/mm² |
125 Ksi / 850 N/mm² |
4% |
45 Ft-lbs / 60 Joules |
341-444 |
4 |
200 Ksi / 1400 N/mm² |
155 Ksi / 1100 N/mm² |
1% |
25 Ft-lbs / 35 Joules |
388-477 |
5 |
230 Ksi / 1600 N/mm² |
185 Ksi / 1300 N/mm² |
- |
- |
444-555 |